PROCESS FLOW DIAGRAM
MAIN FEATURES AND APPLICATIONS
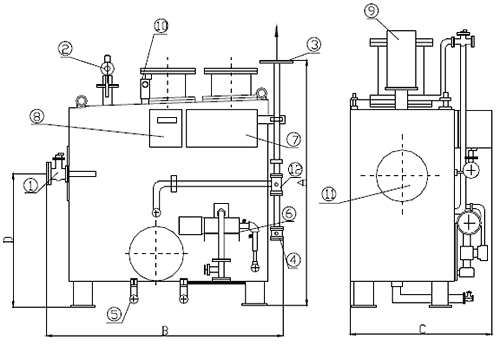
- Oil outlet
- Effluent outlet
- Back flushing line
- Drain
- Pump
- Control panel
- Oil content meter
- Oil probe, 1st stage
- Oil probe, 2nd stage
- Lid
- 3-way valve
PROCESS FLOW DIAGRAM
MAIN FEATURES AND APPLICATIONS
Electrical supply : | 380 VAC / 3 phase / 50Hz 440 VAC / 3 phase / 60 Hz 220 VAC / 1 phase / 50 Hz 115 VAC / 1 phase / 60 Hz |
Compressed air supply: 600-800 KPa Back flushing water pressure: 100-200 KPa |
Genoil Crystal oily water separators utilize a patented, unique process for multi-stage separation of immiscible phases with different densities such as mineral or vegetal oils and water, animal fat and water etc. An innovative separation process combines gravitational and centrifugal forces with surface tension and vortex effects prior to the polishing stage. A highly effective polishing stage enhances performance and minimizes maintenance costs and downtime.
There are no limitations on oil particle size, and Crystal oily water separators feature a method for braking down emulsions. Thus emulsified oil utilized in steel mill processes is reclaimed and recycled with considerable savings. Sludge and solids are collected at the bottom of the first stage, which, in some applications can be fitted with Genoil patented fluidizing devices to facilitate disposal.
Through superior efficiency and engineering, the oily water separators are compact and easy to install wherever space is at a premium. The tank module is precision built, meeting or exceeding the rigorous specifications of classification societies. Oily water separators installed aboard ships have been certified by Germanischer Lloyds and Registrul Naval Roman (Certificate Nos. 32451BUC/27.06.96 and 17/I/3425-DR, respectively). Each unit is tested prior to delivery for complete customer satisfaction and all tests are conducted in accordance with I.M.0. Resolution A.393 (X) / MEPC 60(33).
The automation system ensures unattended operation and features PLC units, self-cleaning oil sensors, and other fail-safe components. The automation is also user-friendly for convenient operation and includes carefully selected components. In custom-built units, Crystal oily water separator can be integrated into complex automation systems being operated and monitored from a central location.
Explosion-proof automation (Class I Div. I) for the oil industry is available upon request. Our team provides technical assistance in special applications, guarantees quality service and helps clients with the installation of larger units. The oily water separators can be custom engineered to suit specific requirements from 600 to 50,000 liters/hour capacities.
Crystal oily water separators typically achieve effluent purities of less than 5 mg/l for 0-100% oil in water mixtures and relative oil densities of up to 0.97. In some applications oil content in the effluent is consistently below 2 mg/l at ambient temperature. In very demanding situations with hydrocarbon densities as high as 0.985 the purity can be reduced to 8 mg/l.
In some US navy and army bases Crystal oily water separators operate in conjunction with Anjan filtering units devised to remove dissolved contaminants. When used in conjunction with Anjan, the effluent purity was below 0.1 mg/l, which is virtually undetectable.
PARTIAL LISTING OF INSTALLATIONS AND TESTIMONIALS
Several Crystal oily water separator units were installed in different locations around the world before Genoil acquired the technology.
OWNER
|
APPLICATION
|
CAPACITY
[LITERS/HOUR] |
QUANTITY
|
INSTALLATION
DATE |
Boyd T. Keogh & Associates Manley, Australia |
Units are operated in conjunction with Anjan filtering equipment for processing industrial wastewater. |
5000 600 |
2 1 |
1995 1995 |
Enviremedial Services Inc. Vista, California U.S.A. |
Oily water separators operate upstream Anjan filtration units for processing wastewater at the U.S. Army base of Camp Pendleton. |
600 1250 5000 1250 2500 5000 |
1 1 1 1 1 |
1995 1996 1996 1998 1998 1998 |
Hydroxyl Inc. Sidney, B.C. Canada |
Unit installed upstream oxygen-based decontamination plant. |
1.250 | 1 | 1996 |
Oil Terminal S.A. Constanta, Romania |
Unit processes ballast oily water from tankers for disposal to sewer. |
50000 | 1 | 1997 |
Administratia Cailor Navigabile S.A. Constanta, Romania |
Bilge water separators installed aboard ships. |
600 600 |
1 2 |
1997 1998 |
Santierul Naval Oltenita S.A. Oltenita, Romania |
Unit processes storm water for disposal to sewer. |
1250 | 1 | 1998 |
U.S. Navy Coronado, California, U.S.A |
In conjunction with Anjan filtering equipment Crystal oily water seperator processes contaminated water in a car wash station. |
1250 | 1 | 1999 |
CE3 Technologies Inc. Edmonton, Alberta Canada |
Units installed in a water treatment plant in conjunction with Anjan and Alfa Laval distillation plants designed to process produced water into pure distilled water. |
20000 | 4 | 2000 |
Centrala Electro Termica Progresul S.A. Bucharest, Romania |
Owned by the Romanian Government, the power plants employ Crystal oily water seperators for processing water contaminated with heavy fuels and bottoms for disposal to sewer. |
20000 | 3 | 2003 |
Ispat Sidex S.A. Galati, Romania |
Units reclaim emulsified oil resulted from steel mill cooling/quenching processes and recyle the oil with important savings. |
10000 | 2 | 2003 |
Centrala Electro Termica Iasi S.A. Iasi, Romania |
Application similar to the one at Bucharest power plant. |
10000 | 2 | 2003 |
Centrala Electro Termica Sud S.A. Bucharest, Romania |
Application similar to Bucharest power plant. |
20000 | 2 | 2003-2004 |